GULHFI Medical Coatings
GULHFI co-workers have more than 30 years experience in large scale production of porous titanium and hydroxyapatite coatings for orthopedic implants like hip joints, knees femoral and tibia implants, shoulder, spine, extremities, ankle and dental implants.
GULHFI is able to apply medical coatings on metallic, plastic and ceramic substrate.
Due its expertise:
GULHFI is able to implement at OEM’s site the most advanced plasma spray coating process integrated in the production line of OEM.
GULHFI medical coatings are fulfilling EU-MDR, US-FDA, Chinese FDA, Korean-FDA Regulations.
The Advantage for OEM:
100% in house coating technology know how
In house process and quality control of medical implant
Strong coating cost reduction using the latest plasma technology
—> Investment pay back 2 -5 years
Significant reduction of implant inventory due to the shortage of production time
GULHFI is now offering the most advanced plasma spray coating technology for medical applications
Porous Titanium Coating
GULHFI is proposing mastered VPS porous plasma titanium coating which is adapted to each specific implants type and customer’s needs.
Porous Cp Titanium as well Ti6Al4V coatings with different topography and micro structures are available
Coating porosity may be varied in a controlled manner between 10% to 50%
Coating thickness range may be between 50 µm to 1’500 µm
Roughness Rz: 35 µm to 350 µm
Titanium coating fulfilling EU-MDR, US-FDA, China-FDA, Korean-FDA requirements
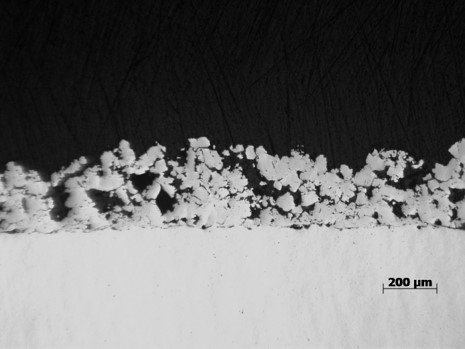
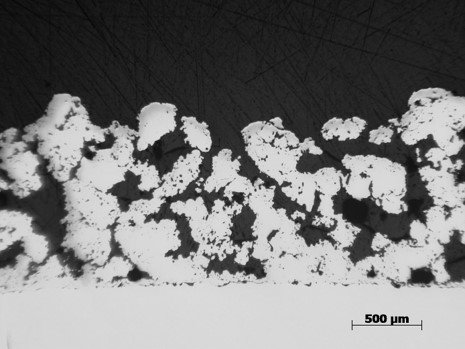
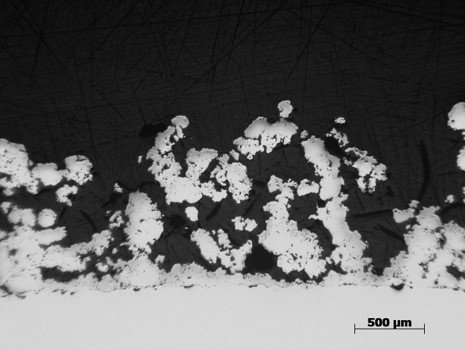
Hydroxyapatite Coating
GULHFI is proposing hydroxyapatite coating which is adapted to any implants type and customer’s needs:
Coating thickness : 20 - 150 µm
Porosity below 5%
High Adhesion strength
High level of crystallinity
Hydroxyapatite fulfilling EU-MDR, US-FDA, China-FDA, Korean-FDA requirements.

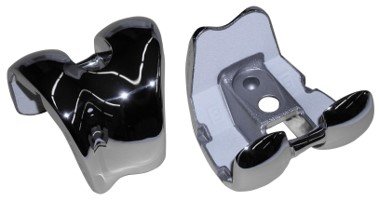
DEBYE LARMOR™ Cascade Torch Technology to Serve Medical Coatings
DEBYE - LARMOR™ is a new generation of cascade low plasma spray fluctuation torches. The optimized plasma
arc stabilization allows to melt precisely and with high stability the injected powder material in the torch,
(titanium, hydroxyapatite, …).
Additionally, the high enthalpy of the plasma torch enable to produce rough (Rz>200 µm) and porous (> 30%)
VPS titanium coating with only pure Argon plasma.
à The use of Helium and Hydrogen free plasma process allows to reduce significantly the plasma gas operation costs.
For large production such costs may be about 50 -100 KUSD per year.
GULHFI Anti-Wear Medical Coating for Bearing Solution
GULHFI Anti-Wear Medical Coating for Bearing Solution
GULHFI has developed the plasma spray technology to apply anti-wear and tough ceramic coating based on different material composition: Al2O3, TiO2, ZrO2+Y2O3 or MgO.
Depending on the OEM’s Hardness/Toughness choice specific ceramic composite material are offered.
Such thick anti-wear coating between 50 micron up to 1000 micron are ideal for a long life implant where CoCr substrate shall be replaced by titanium alloy or another biocompatible substrate with low wear properties.
Any metallic implants based on casting, forged or 3-D printing manufacturing process can be coated with GULHFI ceramic coating.
GULHFI has also developed the polishing processes to master on the ceramic plasma coated surface a very low roughness Ra. Depending on the implant geometry roughness Ra < 0.2 µm are easily achieved, typical Ra values are below 0.05 micron and für cylindrical geometry Ra values < 0.02 micron are achieved.
Typical implants where GULHFI ceramic hard coating may be applied on a bearing surface are: double mobility hip cups, shoulder liner and glenosphere, femoral knee and knee tibia plateau.
With GULHFI anti-wear coating you are avoiding the use of CoCr substrate material:
where a significant amount of people have allergy
is in the material list with potential carcinogenicity
has a strong price fluctuation due to the increasing demand in the automotive industry (electrical battery)
sourcing may be linked to critical countries
Al2O3 + TiO2
Al2O3 + ZrO2
Al2O3 + ZrO2+ TiO2